Hybrid Battery Reconditioning
Dave’s Performance Hybrids is Oregon’s Premier NuVant Certified hybrid battery refurbishing company.
The ability to recondition a battery, save time, money & reduce the impact on the environment. For our customers, and fellow Prius enthusiasts, who want to better understand the process of reconditioning a battery, we’re happy to provide some insight!
How do we recondition a battery?
1. Battery Testing and Reconditioning
This step involves load testing the battery to identify bad cells, performing deep discharging and charging cycles to break up crystalline formation, and retesting the battery to ensure all modules have been successfully reconditioned.
2. Battery Customization and Configuration
In this step, the module capacities are measured and monitored, paired for optimal performance, and used to build a battery according to the customer’s budget and needs. Different warranty options are also offered based on the customer’s requirements.
3. Quality Assurance and Install
This final step involves installing the battery with the verified capacity, ensuring that the customer receives the best value and highest quality product at Dave’s Performance Hybrids.
The diagram illustrates how a series of cells form a module, and a series of modules form a hybrid battery pack.
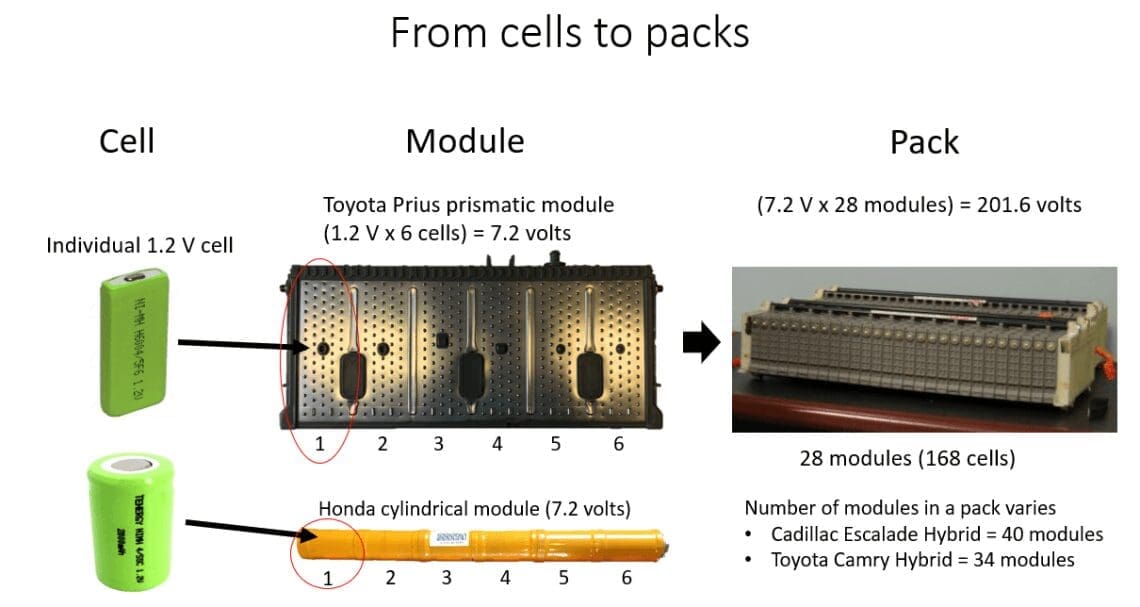
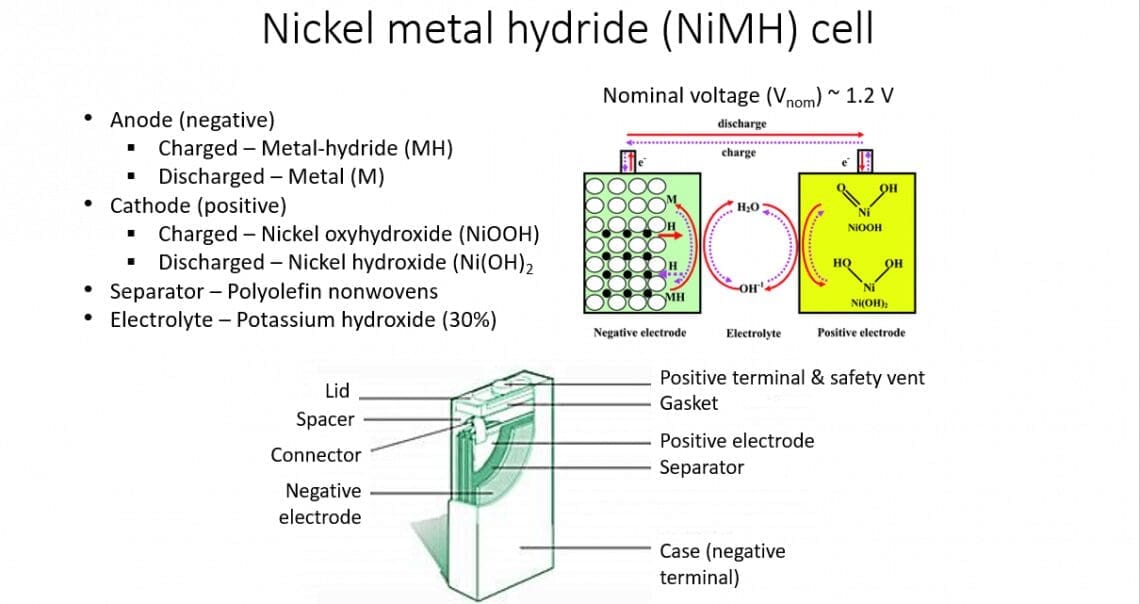
This diagram displays the inner anatomy of a nickel metal hydride (NiMH) hybrid battery cell.
Below is a technical schematic showing the cross section of a hybrid battery cell.
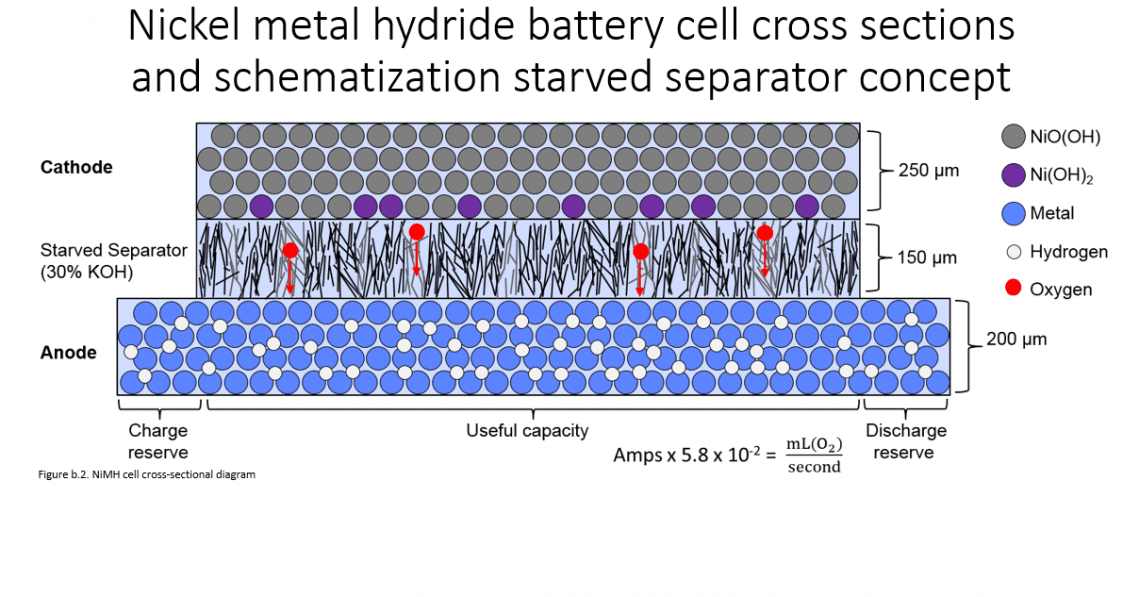
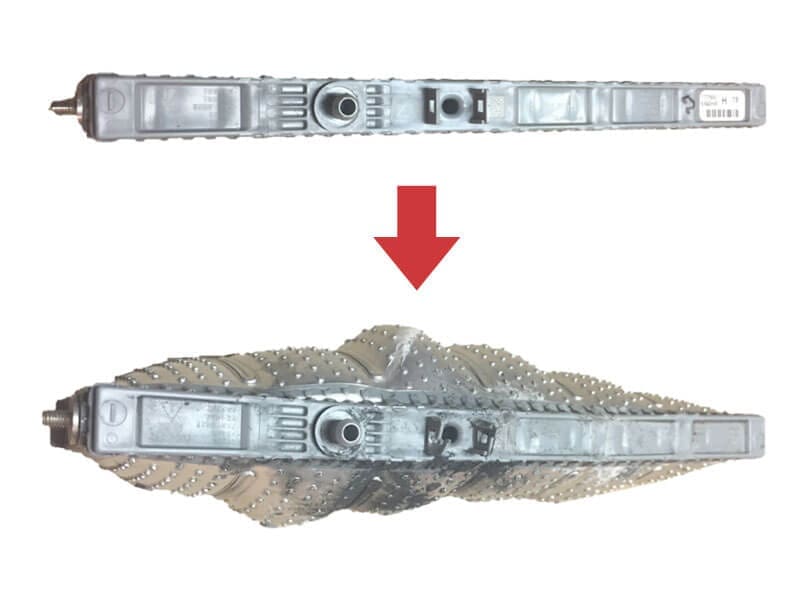
This is an example of what can happen to an overcharged hybrid battery cell.
Here is an image of a Toyota Camry hybrid battery in the process of being reconditioned with our state-of-the-art NuVant Technology.
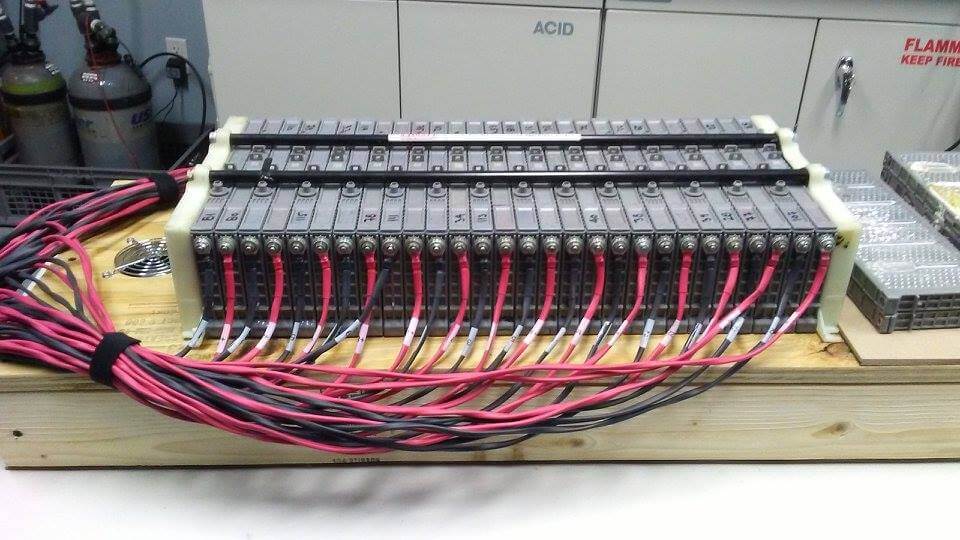
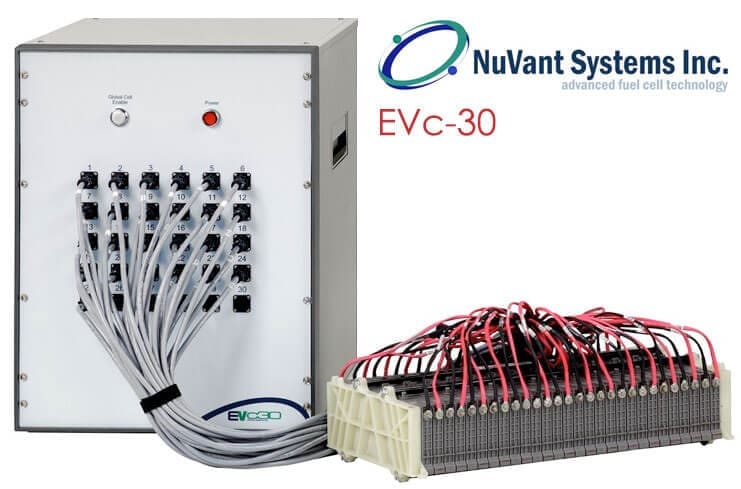
Our NuVant EVC-30 battery reconditioning unit.
How do we recondition a battery?
1. Battery Testing and Reconditioning
This step involves load testing the battery to identify bad cells, performing deep discharging and charging cycles to break up crystalline formation, and retesting the battery to ensure all modules have been successfully reconditioned.
2. Battery Customization and Configuration
In this step, the module capacities are measured and monitored, paired for optimal performance, and used to build a battery according to the customer’s budget and needs. Different warranty options are also offered based on the customer’s requirements.
3. Quality Assurance and Install
This final step involves installing the battery with the verified capacity, ensuring that the customer receives the best value and highest quality product at Dave’s Performance Hybrids.
The diagram illustrates how a series of cells form a module, and a series of modules form a hybrid battery pack.
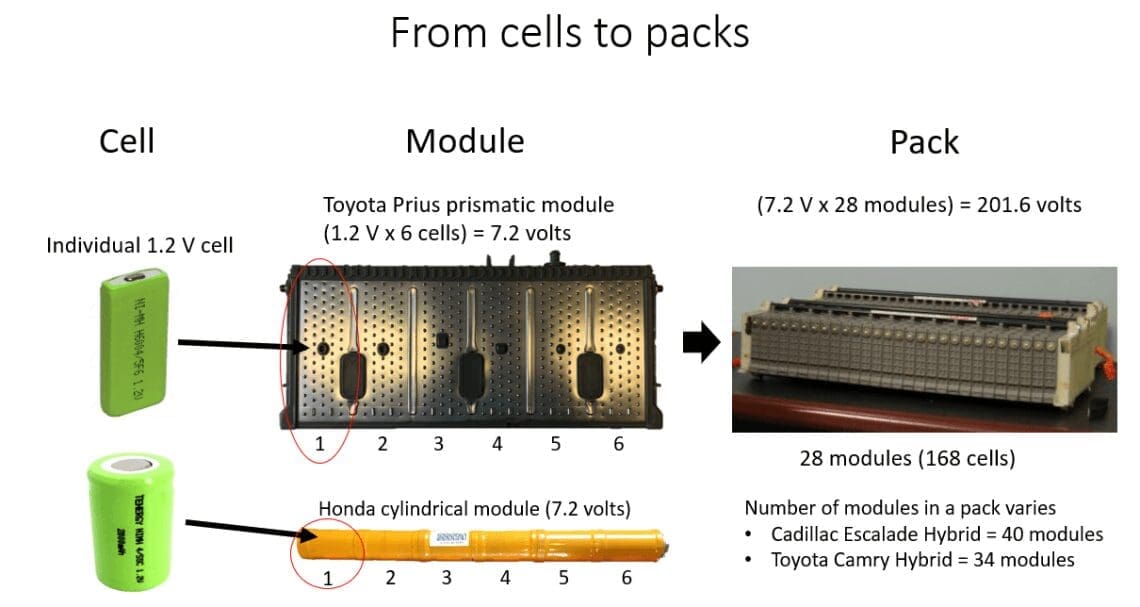
This diagram displays the inner anatomy of a nickel metal hydride (NiMH) hybrid battery cell.
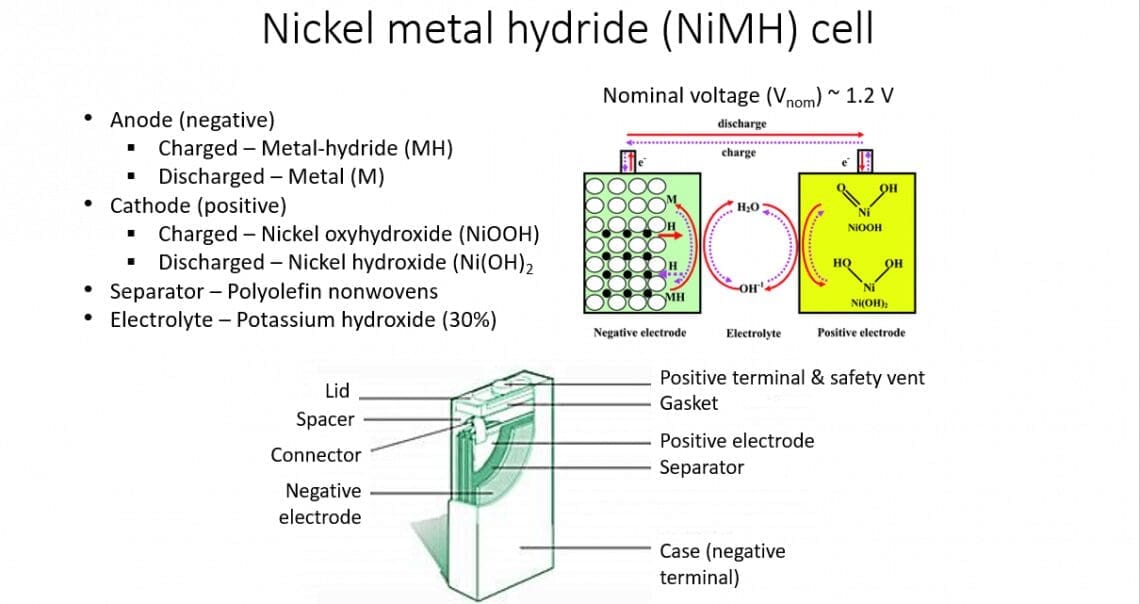
Here is a technical schematic showing the cross section of a hybrid battery cell.
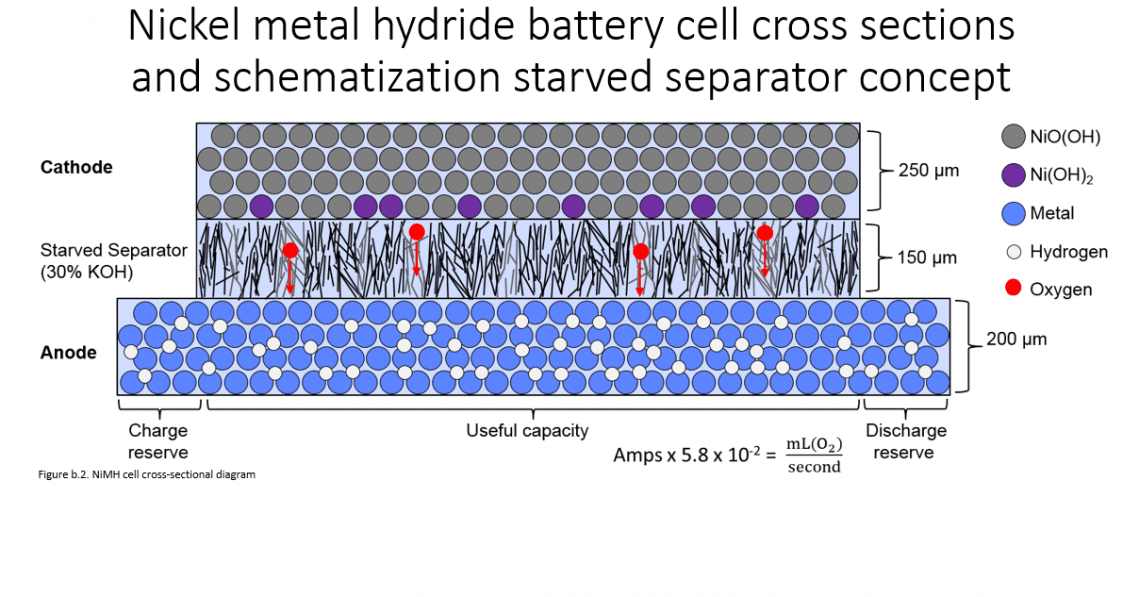
This is an example of what can happen to an overcharged hybrid battery cell.
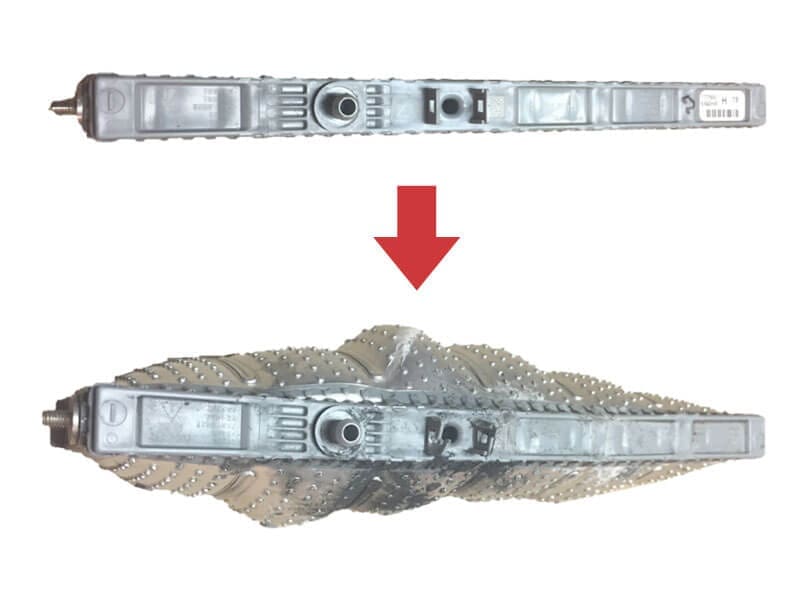
Here is an image of a Toyota Camry hybrid battery in the process of being reconditioned with our state-of-the-art NuVant Technology.
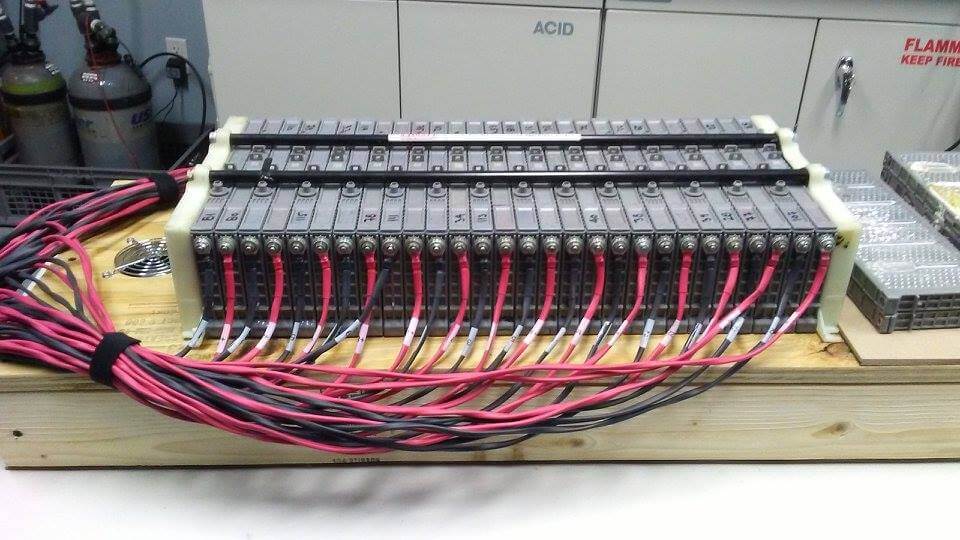
Our NuVant EVC-30 battery reconditioning unit.
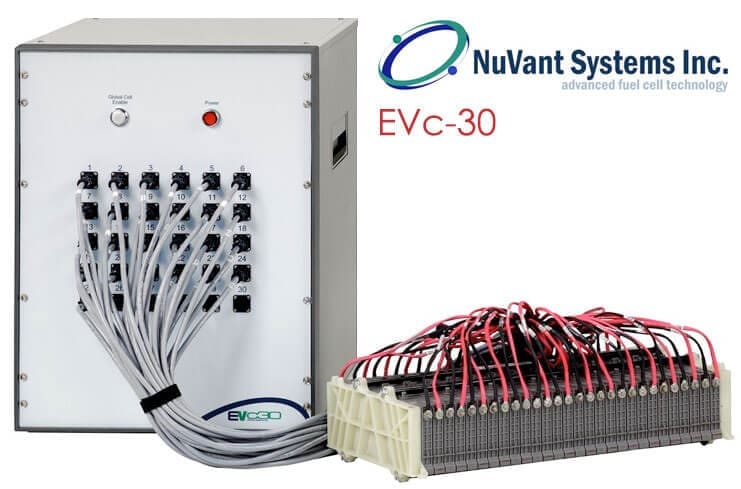